Supply Chain Cost Analysis Skills
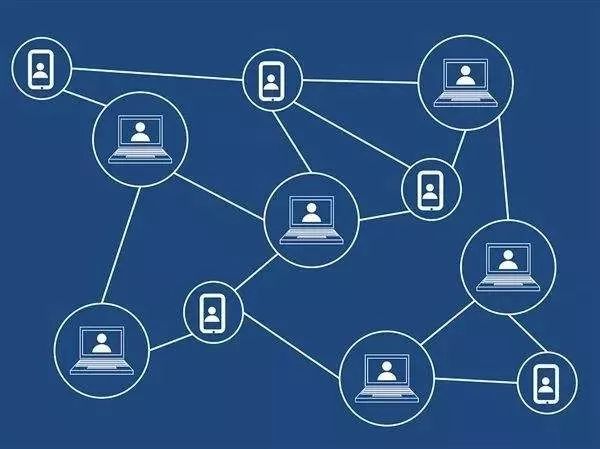
#SupplyChain #Marketing #CostAnalysis
In the face of rapidly changing technology markets and diverse customer demands, many manufacturing supply chains are experiencing unprecedented challenges. Issues like longer component supply cycles, increased sluggish materials, frequent supply shortages, rising material prices and limited production capacity became bottlenecks for electronics manufacturers to optimize supply chains and reduce costs. within the face of severe challenges and fierce competition, more and more enterprises specialise in core competitiveness and survive as a link within the supply chain, which makes supply chain management cross the boundaries of enterprises.
Traditional analysis methods are ineffective when calculating supply chain costs, because most traditional methods only concentrate on internal costs of enterprises, and today's supply chains have crossed the boundaries of enterprises, and provide chain management has transformed into cross-organizational collaboration and management. Therefore, the price analysis of the provision chain must transcend the "four walls" of the corporate, concentrate to the general structure of the provision chain, consider various factors as a full, and grasp it from the next level.
Three levels
Based on the most effective practices of a number of the world's top 500 companies and therefore the research results of experts, the author believes that the analysis of the availability chain should start from three levels:
1、Direct cost, which refers to the value of manufacturing each unit of product, including raw materials, parts, labor and machine costs. These costs are mainly determined by the worth of raw materials and labor.
2、Activity costs, which see the prices incurred in managing the assembly and delivery of products, and these costs arise from the company's organizational structure.
3、Transaction costs, including all costs incurred in processing supplier and customer information and communication. These costs are mainly derived from the interactions between the corporate and other partners within the supply chain.
Costs take different forms under different supply chain processes and states. as an example, the acquisition of components, on the surface, the price is principally reflected within the terms, which could be a direct cost, but different components may involve some value-added services, so there's a service cost; at the identical time, if you purchase substandard products, you wish to Return and exchange, in turn, will involve operating costs and transaction costs.
Take a particular case: a Chinese manufacturer purchases a specific device from Singapore and conducts a value analysis of it. The unit price of the device is 10 yuan, and if you purchase 10 at a time, it only costs 4.5 yuan each. the rise within the purchase quantity obtains a price discount, which reduces the direct cost, but the price in other aspects may increase, like the transaction cost with the supplier, the logistics cost, the operation cost of customs duties, etc. Attrition risk also increases. additionally, since the manufacturer doesn't need the ten devices immediately, the surplus devices have to be stored within the warehouse, leading to increased storage-related expenses and inventory holding costs. Of course, if it's only one purchase, the procurement interval is extremely long, and also the direct cost and transaction hike.
It is seen from this case that the price analysis of the provision chain has to consider the general situation from many aspects, conduct in-depth analysis of the specific and implicit costs generated by each link of the provision chain, and optimize the structure of the provision chain to scale back costs.
Four areas
We can combine these three cost levels with the supply chain-production-relationship dimension to establish a supply chain-based cost analysis framework. Specifically, the focus of supply chain cost analysis is distributed in four areas: product and marketing network formation, product design in supply chain, production network construction and supply chain process optimization.
1st area
It is the formation of a product and marketing network, involving basic decisions such as which products and services to offer and the selection of relevant partners. In this area, it is necessary to focus on the time to market, customer needs, product design, sales network layout and depth of relationship with partners, etc. The costs are mainly concentrated in two levels: operating costs and transaction costs. The sales of products are usually affected by factors such as culture, economy, consumption habits and customs in various regions, and each product has a specific life cycle. From development and listing to withdrawal from the market, the time when a product is popular in the market is often unpredictable. Therefore, the supply chain costs involved in this area often have greater uncertainty.
For example, a certain type of product does not sell well in the southern region, and has accumulated inventory for half a year, and is expected to withdraw from the market soon; while this type of product is a hot-selling product in the northern region, often out of stock, and can continue to be sold for at least half a year. So, how do you transfer between regions to ensure overall low inventory costs without compromising customer service? Too much adjustment will lead to high operating costs, such as logistics costs and labor costs; too little adjustment will cause customer churn costs, out-of-stock costs and inventory holding costs to rise.
It is wise to infer the sales ratio distribution and service requirements of each product line in each region based on the historical sales data of various products, the market forecast of sales personnel, the degree of customer fussiness, and the possible risk of inventory holding costs. As a basis for designing supply chain activities, such as whether to need rapid response, whether to require suppliers to manage inventory, whether to need logistics information system docking and so on.
2nd area
Is the product design in the supply chain, involving transaction costs, activity costs and some direct costs. Different products and services have different requirements, which largely determines the depth of cooperation with supply chain partners. For example, some products and services require related suppliers to cooperate closely in the design stage. The transaction cost when supply chain partners first establish a partnership will account for the majority of this part of the cost, especially for some products that require suppliers to develop collaboratively, strategic investment in such suppliers may be required in the early stage, resulting in very high However, due to the long-term close relationship established with each other, this investment will be rewarded through the reduction of operating costs and transaction costs in the later cooperation.
On the other hand, the use of different types of devices in product design will also involve different costs, such as the use of proprietary devices, the cost of communication with suppliers and the cost of procurement operations may be relatively small, but the cost of after-sales maintenance services in the future high, and the procurement risk is high. Therefore, in product design, the cost involved should be considered comprehensively for device selection.
3rd area
It is the construction of production network, mainly refers to the network layout between manufacturers and their suppliers and foundry partners, which involves the transaction costs of communication and information exchange between manufacturers and suppliers and foundry partners, management of supply and Activity costs of the production process and direct costs such as the price of components and services.
Every manufacturer in the supply chain is trying to locate its production base close to both major customers and important suppliers, while expecting to keep production costs low. To achieve these goals, manufacturers should comprehensively analyze the total cost based on the characteristics of the product, based on factors such as location, complexity of technical requirements, ease of access to raw material supply, and customer demand response. In this area, we should not make rash judgments based solely on the level of individual cost categories. As a result, the overall layout of the production network is uneconomical and lacks cost competitiveness. For example, some regions have low labor costs and can obtain lower direct costs, but remote locations and inconvenient transportation will bring higher operating costs and transaction costs; while some regions have high production efficiency and lower operating costs and transaction costs, But higher labor costs and land costs will lead to increased direct costs.
4th area
It is the process optimization of the supply chain, including the optimization of the procurement process, production process and price process. This section focuses on cost-cutting measures, including reducing direct and operating costs. Analyzing the production process and inventory sweet spot of the whole supply chain, analyzing the reasons for the high scrap rate, redesigning the production process or optimizing the order fulfillment between the company and the supplier, etc. link.
Eight ways
The relative importance of the three cost tiers depends largely on the products and services the manufacturer provides. For example, products with a longer life cycle require lower transaction costs in supplier selection, relationship building, and product and process design; products with a shorter life cycle or technology cycle require higher investment costs in the initial decision-making stage , and because these products usually survive in the market for less time than product development, manufacturers face a higher risk of unrecoverable investment, which determines that they must actively manage transaction costs and operating costs. Overall, there are eight ways manufacturers can improve supply chain costs.
1. Obtain the support of senior management.
Without high-level support, supply chain cost management will become a luxury. But to get this support, top management must fully understand the value and significance of supply chain management to the bottom line.
2. Select the appropriate information system.
Information systems can help identify opportunities for coexistence with other supply chain members within the relevant scope, such as cost leverage, knowledge integration, and technology sharing. In addition, a good IT system can provide information on where improvements can be made to reduce costs, use resources efficiently, and optimize where inventory is distributed.
3. Determine the total cost drivers.
In a specific supply chain, analyze what elements make up the total cost. Drivers of total cost can vary by geographic location and may include logistics, shipping, inventory, lead times, and poor infrastructure, lack of trained staff, substandard suppliers, or the production of some special products. Influence. If analyzed on a global scale, total cost drivers may also include tariffs, currency exchange rates, political factors, and geography.
4. Establish a model of the main cost components of the supply chain as soon as possible.
In a global supply chain environment, cost models should also be adjusted for different countries and regions. Techniques for establishing cost models include learning curve analysis, empirical effect analysis, price-capacity analysis, installation cost analysis, due cost analysis, process comparison analysis, and cost decomposition.
5. Develop a strategic cost management plan.
The objectives of cost management must be clearly recognized and a plan for how to achieve them must be developed.
6. Build efficient cross-functional teams.
Since different departments need to be involved in the process of implementing cost management, effective cross-functional teams are critical to the implementation of cost management.
7. Analyze the total purchase cost.
Often, supply chain cost reductions are not primarily achieved by lowering prices. Price is an important cost factor, but not the only one. Lowering costs has more potential than simply lowering prices, and is sometimes much easier to implement than lowering prices.
8. Conduct effective performance appraisals.
Without an effective performance evaluation mechanism, companies do not know how far they have achieved, how far they have been compared to the past, and how they will develop in the future. The performance measurement mechanism should be based on the comprehensive management of strategic costs that are critical to success. Start by identifying what factors are critical to success; then measure the degree of completion on the assigned metrics. The results of the assessment can reflect success or failure and identify problems, and it is also the basis for taking corrective actions.
Leave a comment