Why is it difficult to reduce enterprise supply chain costs?
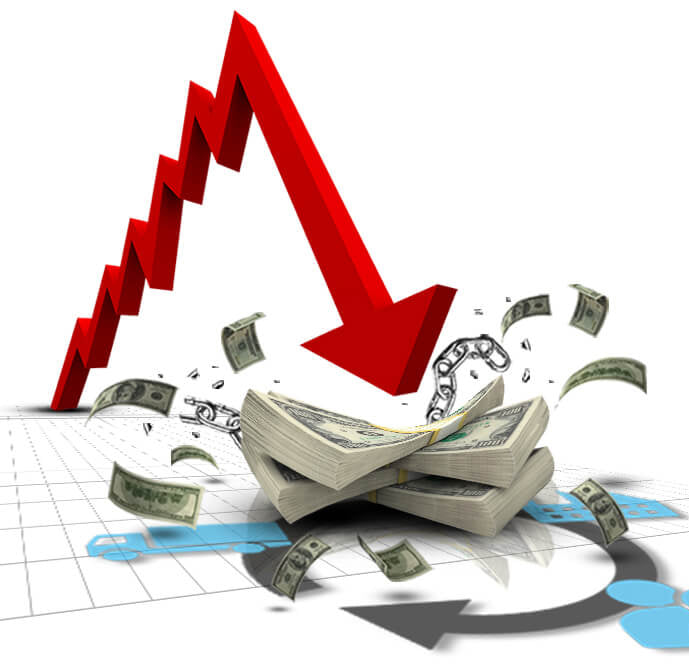
#SupplyChain #BusinessManagement
Enterprise supply chain costs mainly include:
- purchase cost;
- Cost of production;
- warehousing costs;
- transportation cost;
- Inventory costs;
- out-of-stock costs;
- quality cost;
- management costs.
After years of management improvement, the above-mentioned single cost has been reduced to the greatest extent. Now, the difficulty of supply chain cost management is that we not only have to establish a management method to reduce the cost of each individual item, but also the balance between the individual costs. We often find that some individual costs of enterprises are reduced a lot. However, the total cost of the company's supply chain has increased instead of falling. This is why?
Purchasing costs have decreased, which costs will increase?
A company's procurement costs are reduced, and quality costs may increase. This should not be difficult for everyone to understand - what is the biggest risk of buying cheap materials.
Production costs have decreased, which costs will increase?
Production costs refer to various production expenses incurred for producing products or providing labor services, including various direct expenditures and manufacturing expenses.
1. Direct expenses include direct materials (raw materials, auxiliary materials, spare parts, fuel and power, etc.), direct wages (salaries and subsidies for production personnel), and other direct expenses (such as welfare fees);
2. Manufacturing costs refer to the various costs incurred by the branch factories and workshops in the enterprise for the organization and management of production, including the salaries of the branch factories and workshop managers, depreciation costs, maintenance costs, repair costs and other manufacturing costs (office costs, travel expenses, labor insurance, etc.).
To reduce production costs, it is necessary to increase a certain amount of inventory costs. The more adequate the stock of raw materials is. The less frequently the production line is temporarily adjusted, the less overtime is required. With proper stockpiling of finished goods inventory, the efficiency of the production line will be improved.
Warehouse costs have decreased, which costs will increase?
First, warehousing costs include:
Custody fee
Warehouse management staff wages and benefits
Depreciation
Rental fees
Maintenance fees
Handling fee
Management costs
Storage loss.
Warehousing costs are reduced, and out-of-stock costs may increase. Warehouse operations are more prone to errors (wrong goods received, wrong materials sent, inaccurate data), resulting in an increase in production costs. In addition, the procurement cost will also increase, because the number of purchases is not large.
Shipping costs have decreased, which costs will increase?
Shipping costs are reduced and inventory costs may increase. Should the demand for a month be shipped in one shipment or in multiple shipments? In addition, the transportation cost is reduced, and the transportation time limit, on-time rate, and loss rate will be affected. The cost of sales will increase.
Inventory costs have decreased, which costs will increase?
What does inventory cost include? Inventory holding costs can be divided into operating costs, opportunity costs, interest costs, and sluggish costs.
1. The operating cost mainly refers to the storage cost.
2. What is the opportunity cost? The enterprise loses the investment income that the working capital can bring because it needs to hold a certain inventory, which is the opportunity cost of the inventory.
3. Interest cost refers to the fact that sometimes a business obtains inventory by borrowing money. If the inventory item brings to the company less than the interest on the loan. The difference between the periods is the interest cost.
The cost of inventory is reduced, and first, the cost of out-of-stocks increases. Second, procurement costs, production costs, and transportation costs will increase. Purchasing costs should be directly proportional to the quantity purchased. The larger the quantity purchased, the more favorable the purchase will be. In addition, any supplier has a minimum purchase limit. What should the purchasing department do when the supplier's minimum purchase quantity is our demand for two months?
For a production line, the fewer the number of single products produced and the higher the frequency of production changes, the higher the production cost.
Out of stock costs are reduced, which costs will increase?
The out-of-stock cost should be discussed separately from the out-of-stock cost of raw materials and the out-of-stock cost of finished products.
stock-out cost of raw materials
Out-of-stock costs for raw materials include:
(1) Loss of stopping and waiting for materials (daily fixed cost of production line);
(2) Overtime expenses for catching up with the construction period due to lack of materials;
(3) Additional costs for urgent procurement (air freight);
(4) The additional cost of safety stock, etc.
Out-of-stock cost of finished goods
Out-of-stock costs for finished goods include:
(1) Additional charges for postponing sales to the next period;
(2) Loss of sales order cancellation;
(3) Loss of customer costs;
(4) Additional costs for developing new customers
Obviously, the cost of out-of-stock is reduced, and the cost of inventory is likely to increase.
Quality costs have decreased, which costs will increase?
First, what is the cost of quality. Quality cost refers to all the expenses paid by the enterprise to ensure and improve the quality of products or services, as well as all the losses caused by failing to meet the product quality standards and failing to meet the needs of users and consumers.
Quality cost = prevention cost + appraisal cost + internal loss cost + external loss cost
1. Prevention costs are various costs incurred to reduce quality loss and inspection costs, and are the costs of some activities carried out to meet quality requirements before the results are produced. It includes quality management activities and administrative costs, and quality improvement measures. , quality education and training fees, new product review fees, quality information fees and process control fees;
2. The appraisal cost is the cost of testing, evaluating and inspecting the quality of the product according to the quality standards. It is the cost of testing activities in order to evaluate whether the results meet the requirements after the results are generated, including departmental administrative fees, materials Process finished product inspection fee, inspection equipment maintenance fee and depreciation, etc.
3. Internal loss refers to the loss of defective products, repair costs, downtime losses and re-inspection costs before the product leaves the factory;
4. External losses are various losses caused by quality problems after the product is sold, such as claims losses, breach of contract losses and "three guarantees" losses.
To reduce the cost of quality, procurement costs and production costs must increase. That is to say, the price of inspection-free raw materials will not be the cheapest. The more advanced the equipment on the production line, the lower the possibility of quality problems. Of course, equipment costs will increase.
Management costs are reduced, which costs will increase?
Management costs should include wages and benefits, training costs, software costs, administrative logistics costs, etc.
Generally speaking, the management cost of foreign-funded enterprises is higher than that of private enterprises.
If the management cost of an enterprise is unreasonably lowered, several other costs and expenses may increase.
In a word, for the senior management of the enterprise, the cost management of today's supply chain is more like holding down multiple gourds and scoops in the pool. The difficulty is that when we press this scoop, that gourd rises, and even more gourds rise. The important thing is to establish a good supply chain system, think overall, and optimize the design.
Leave a comment